Preparation of a polymeric aggregate of unsaturated Poly ester with sawdust and studying its physical and mechanical properties
Abstract
In this study a type of polymeric composites from melting poly Unsaturated polyester as a basic substance with powdered sawdust was prepared, studying some of it is mechanical properties, which was included: Impact Strength (I.S), Yong modulus (E), Brinell hardness (B.H) and compression Strength (C.S). Polymeric composites before and after reinforcing were studied by comparison between them. It was noticed increasing resistance of Yong modulus (E), Impact Strength (I.S), Brinell hardness (B.H) and compression Strength (C.S). Also, It is studied the effect of some acids like (HCl, H2SO4, HNO3) with concentrations (0.5 N; 1N and 1.5N) respectively. Some physical properties were studied as absorbance and poly propylene's diffusion coefficient before and after reinforcing. The results showed increases in values of these properties with increasing concentration of acid and time of polymer's immersion in the acidic solution.
Keywords
polymeric composites, polyester, powdered sawdust, Diffusion Coefficient
Introduction
As a result of scientific progress featured need, certain specifications polymer materials can be obtained from one type of polymer. This appeared in the blending of two or more polymers and get a mixture of industrial specifications unwanted polymers, polymeric mixtures are known as the result of mixing two or more polymers physically merged so that the resulting mixture has common characteristics between vehicles (Utracki & Sperling, 1990), Many research that indicates the importance of the use of composite materials, encourage researchers to work in this area, wood has been used since ancient times in construction continues to be used in construction and industry as a construction material, Widely used due to low cost and easy accessibility (Dobreva, Nenkova, & Vasileva, 2006; Shaker, Al-Awsi, Khamis, Tolaifeh, & Jameel, 2018).
To strengthen the fragile polyester by adds aluminum as reinforcement material that gave polyester strength and durability (Padmanabhan, Arun, Sivarama, & Reddy, 2016), Reinforcement of unsaturated polyester with carbon fiber by different weighting ratio the results showed improved in thermal conductivity and mechanical properties with increasing the ratio of carbon fiber (Abed, 2017; Al-Awsi, Chalap, & Abdulhussein, 2019; Chalap & Al-Awsi, 2019; Islam, Mahdi, Hosur, & Jeelani, 2015).
Effect of fine silicon carbide (SiC) powder with (0,3,5,7) wt % on the thermal conductivity and mechanical properties of unsaturated polyester composite in the presence of a fixed amount of chopped glass fiber. The hand lay-up technique was employed to prepare the required samples. Results showed that tensile, impact strength and thermal conductivity increased with increasing the weight fraction of reinforced materials (Chillab, Talib, & Al-Awsi, 2019; Musa, Aghajan, & Majed, 2018).
Mechanical properties of basalt and E-glass fiber composites was performed. Results of apparent hoop tensile strength test of ring specimens cut from tubes and the interlaminar shear stress (ILSS) test are presented. Tensile tests using a split disk method provide reasonably accurate properties with regard to the apparent hoop tensile strength of polymer reinforced composites.
Comparison between the two tubes showed higher basalt fiber composite performance on apparent hoop tensile strength (45% higher) and on the interfacial property interlaminar shear stress (ILSS) (11% higher). New data obtained in this work on basalt fiber composite tubes confirm the literature for basalt fiber composite with other geometries (Lapena & Marinucci, 2017). Improvement of some properties of NBR reinforced by short aramid fiber. The usage of bonding systems such as resorcinol /hexa methylene tetramine/silica (HRH) enhances the fiber/NBR adhesion and maintains optimum composite strength properties.
Mechanical properties of composites, namely, tensile strength, hardness, and modulus at 100% elongation, compression set can be enhanced by adding aramid fibers (Mohammed, Elangovan, & Subrahmanian, 2016). Studied the preparation to prepare sheets of epoxy composites reinforced with two types of glass fibers (random, bidirectional and with the two types of glass fibers as a sandwich), the number of glass fibers was 1, 2 and 3 layers with volume fraction 25%.
Thermal conductivity results of epoxy composite increase with increasing glass fiber layers, whereas thermal conductivity results of the epoxy composites reinforced with random glass fibers show lower values of thermal conductivity than other two composites in relative. The glass fibers orientation for glass fibers important role of effect in transferring the thermal flux through the fibers as it increases in general for the three types with increasing the number of glass fibers layers in various percentages according to the direction of the thermal flux through the fibers. Hardness (shore D) tests results of epoxy composite increases with increasing glass fiber layers (Abdullah, Mahmood, & Algidsawi, 2017).
Unsaturated polyester resin reinforced by palm fiber extracted from different locations (Trunk, Petiole (bases leaflet date palm tree), Rachis and Panicle) of the palm tree in Iraq. The study included the effect of fiber length and their location within the plant as well as the percentage of the volume fraction (0%, 10%, 20%, 30%, and 40%) on the mechanical properties, thermal and acoustic insulation for all the samples prepared.
The results showed that mechanical as well as the thermal and acoustic insulation properties increase with increased the volume fraction for all kinds of the date palm fibers, whereas decrease with increased fiber length also those properties depend on the nature of the date palm fibers as the following sequence (samples reinforced by petiole fibers > samples reinforced by trunk fibers > samples reinforced by rachis fibers > samples reinforced by panicle fibers) (Sihama, Salih, Al-Kaisy, & Imad, 2013).
The effect of adding Alumina as a strength phase to unsaturated polyester resin has studied, in this study, the unsaturated polyester resin strengthen with different percentage (2.5, 5, 10)% from Alumina has been executed, and then the mechanical behaviour of prepare samples has been studied. The tests include (bending, density, water absorption, hardness and Modeling ANSYS) and the results show that composite materials have less density al 10% Al2O3 which is decreased by 6% and largest results for bending which is 60% and also less water-absorbing which is 0.6%.
On the other hands adding Al2O3 in any ratio (2.5, 5, 10)% increase the hardness of unsaturated polyester resin as well as reduction the strain as shown in ANSYS Modeling (Al-Khafaji, Sattar, & Mohson, 2018; Ewaid, Abed, & Al-Ansari, 2019; Ewaid, Abed, & Al-Ansari, 2019).
Aluminum powder on the mechanical properties of unsaturated polyester which is manufactured in the Turkey, as function of the percentages of aluminum powder (0.5%, 0.8%, 1%, 1.5%, 2%, 2.5%), at particular size (150) µm, were investigated through several variables, such as, young's modulus, strength, elongation and the flame resistance. The obtained results were the properties (unsaturated polyester /aluminum powder) composites were analyzed as a function of the filler amount. All prepared composites showed improved filler dispersion in the unsaturated polyester matrix (Jassim & Mohammed, 2018).
Strengthened the Epoxy with fiber glass which reinforced supported with sisal's fiber for its high strength and lightweight and biodegradable then evaluated its mechanical properties such as tensile strength and compression strength and hardness tests, the results indicated that the integration of sisal fibers with glass improves mechanical properties (Kumar, Kumar, Rajashekhar, & Ramakrishna, 2018) Mechanical and thermal properties of composites, consisted of unsaturated polyester resin, reinforced by different kinds of natural materials (Orange peels and Date seeds) and industrial materials (carbon and silica) with particle size 98 µm were studied.
Various weight ratios, 5, 10, and 15 wt. % of natural and industrial materials have been infused into polyester. Tensile, three-point bending and thermal conductivity tests were conducted for the unfilled polyester, natural and industrial composite to identify the weight ratio effect on the properties of materials. The results indicated that when the weight ratio for polyester with date seeds increased from 10% to 15%, the maximum Young’s modulus decreased by 54%. When the weight ratio was 5%, the maximum Young’s modulus, yield stress and ultimate tensile stress (Abdulhussein & Al-Awsi, 2019; Dahad, Hasan, & Alwan, 2018).
Materials and Methods
Practical part
Apparatus uses
After drying the sawdust in the 90ᵒC in oven for three hours, crushed as a powder and placed in metal molds made of locally iron (10 cm x 20 cm) and the ratio (12, 22, 32) wt % (to unsaturated polyester molten in 165ᵒC and pressure of 1.5 tons, then added 2% of methyl ethyl ketone peroxide(MEKP) as curing agent to make gel material cured in room temperature, and obtained the weight ratio from the following relationship: (Schwartz, 1984)
( )composite fibers weight ratio.
(Wc,Wm,Wp) mass of sawdust, base material and composite respectively
Then he pressed the modules to ensure avoid of inside air gaps then after completed casting process in 24 hours to post curing and extracted from the mold, then cut to pieces by standard specifications (ASTM) for each test. It was prepared three samples of composes fiber sawdust with unsaturated polyester Table 1.
Unsaturated polyester weight (gm) |
Sawdust weight (gm) |
Volume(mm) |
No. |
Samples |
---|---|---|---|---|
10 |
- |
150 |
- |
unsaturated polyester |
8.8 |
1.2 |
150 |
1 |
unsaturated polyester+ sawdust |
7.8 |
2.2 |
150 |
2 |
unsaturated polyester+ sawdust |
6.8 |
3.2 |
150 |
3 |
unsaturated polyester+ sawdust |
2-Acidic solutions for each: HNO3, H2SO4 , HCL
Prepared acidic solutions of (HCl, H2SO4, HNO3)
With concentrated of (0.5N; 1.0 N; 1.5 N) for each acid then chopping the samples reinforce and non with sawdust into small cuboid-shaped models samples and put all pieces in acidic solutions for all three concentrations at room temperature, and then Weighed forms graduating from lotions and weighing every 7 days and for a period of 120 days.
Apparatus used
Measured the yonk coefficient by using tri-point test apparatus (3 Point test) equipped by ELE-England company, shock measured with a Garbee apparatus equipped by Tokyo Koki company Seizosho, LTD, and using a hydraulic piston type (D-6700) provider from a WOLPERT – Germany company to measure Brinel hardness mm (HBr Brinel) and compressing.
Results and Discussion
The most important physical properties that have been studied in this research are
Young’s Modulus
The study in dimensions change of the polymer as a function of stress as important physical property for all polymers (Stress) when effort stress on polymer sample at a constant speed and then measure the distortion, either in terms of the change in size or length or change in area and can identify the behavior Polymer under stress and can obtain information about the characteristics of polymer in terms of strength and durability and flexibility of curve stress – tensile strength (stress-strain curve) and the maximum effort can handle form, and maximum elongation may occur in model, and mechanical information task (Abood, Farhan, & Fadhil, 2015; Topouzi et al., 2017) Stress means power inflicted on a unit area of cross-section of the form and symbolizes his symbol (σ)
Either strain (ε) is the amount of elongation form as a result of exposure to stress relative to the original length of the sample.
Sing Tri-Point test loading measurements system were obtained representing the relationship between stress and aberration of unsaturated polyester before and after reinforced with sawdust, where select value (elasticity coefficient) yonk coefficient mile curve, which represents the ratio between stress and tension. The following relationship (E).
Figure 1 shows the relationship between the stress and tension of polymer before and after reinforcement at 25°C where appropriate stress (load)is directly proportional to stretching, and the release of the influence of loaded return to the first situation, it means within the limits of the flexibility strain proportion is directly related to stress.
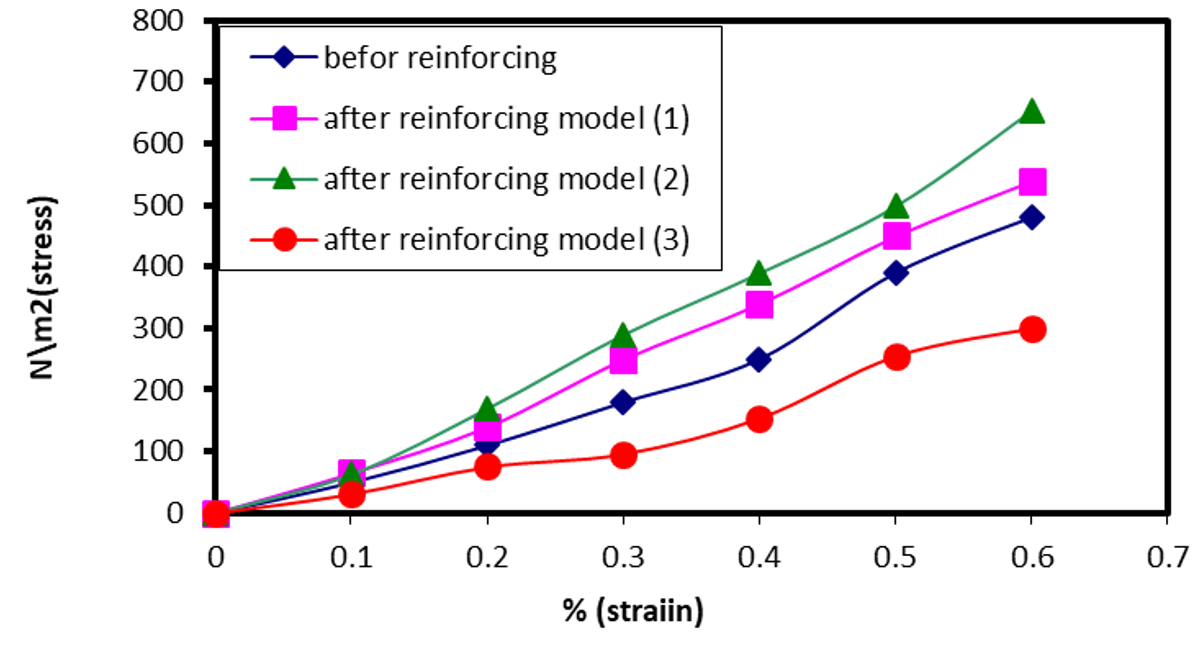
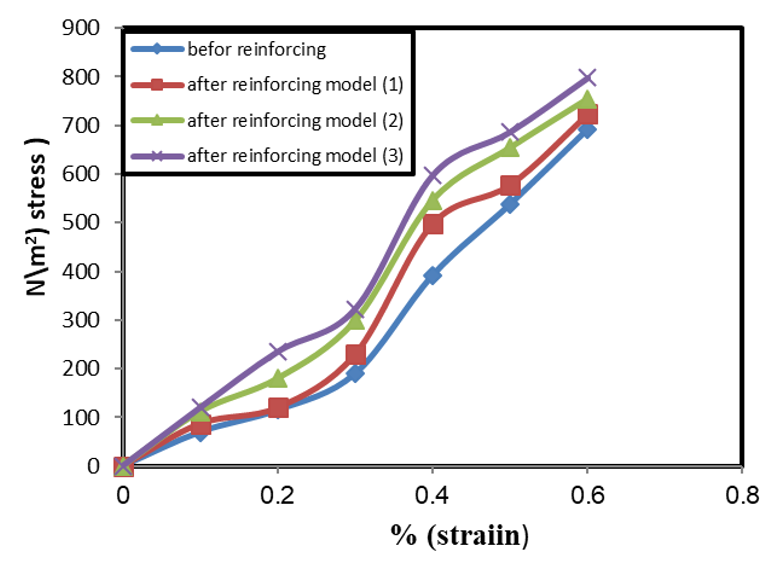
Note the effect of increasing temperature on flexibility coefficient in Figure 2 where the flexibility coefficient decreased with increasing temperature when compared with the Figure 1.
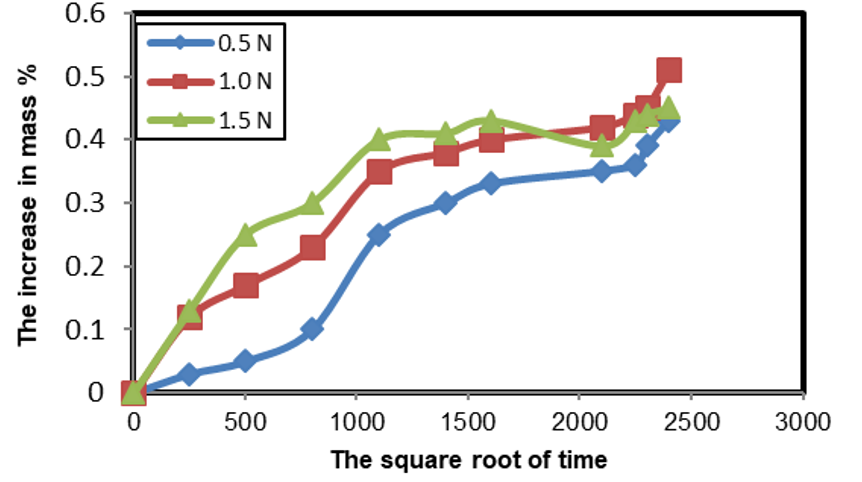
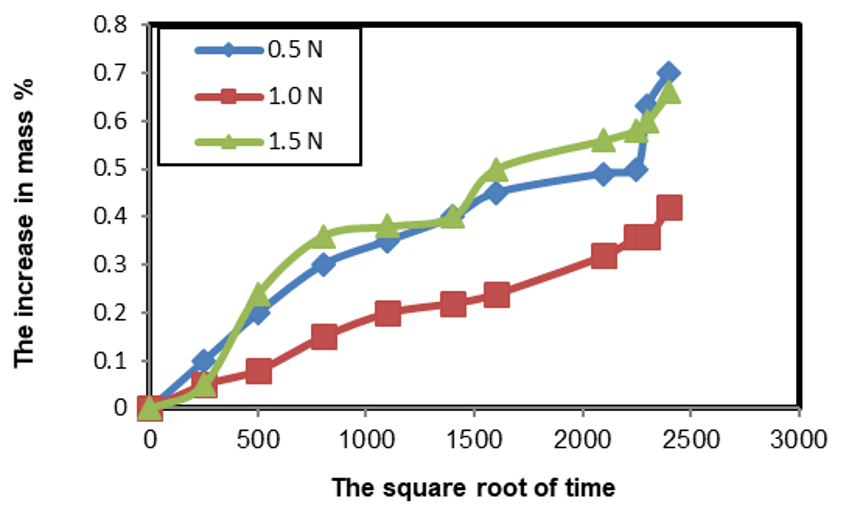
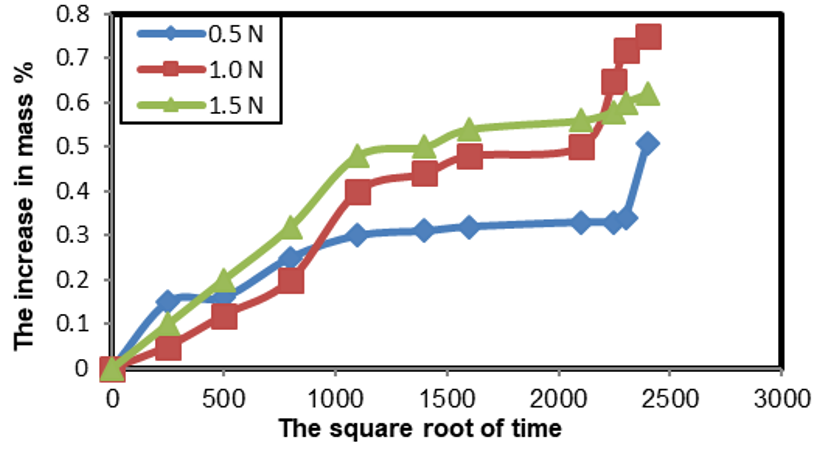
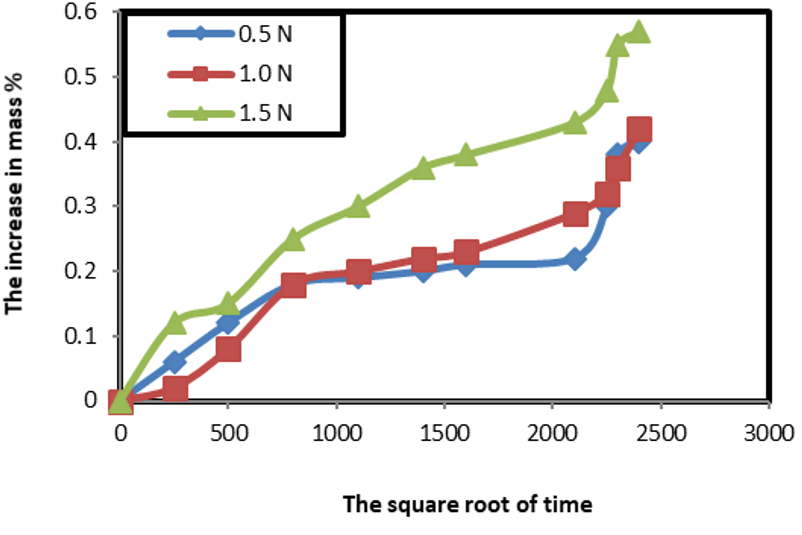
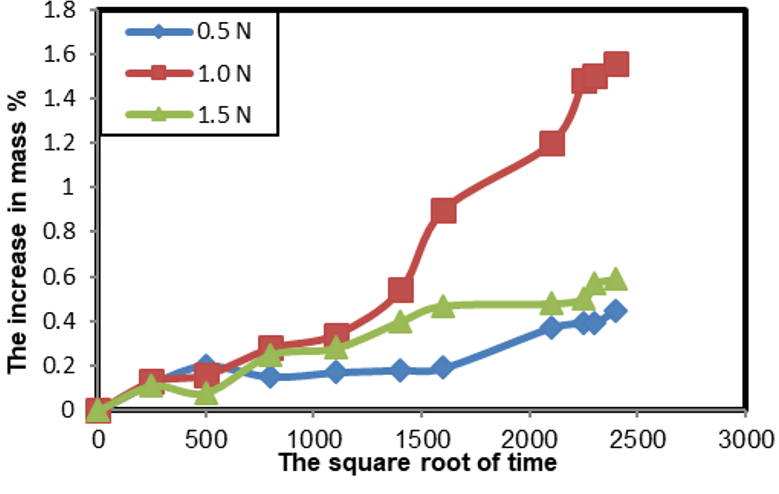
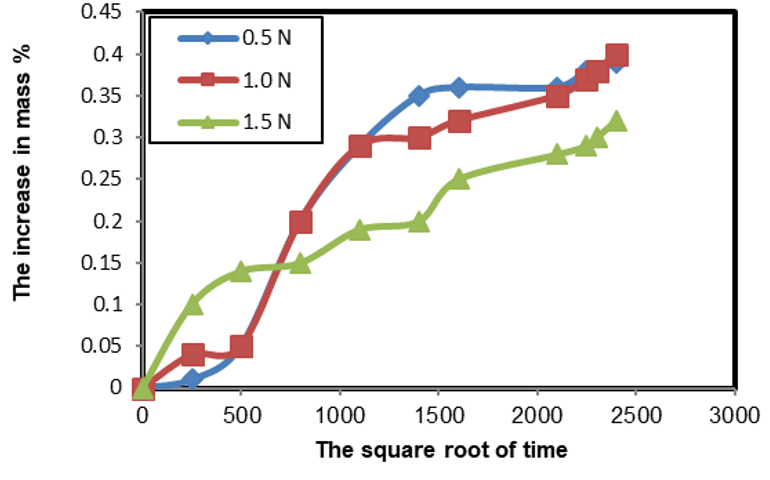
polymer after change(sample3) |
polymer after change(sample2) |
Polymer after change(sample1) |
polymer before change |
yonkco factor |
---|---|---|---|---|
586.4676 |
1030.624 |
894 |
718.1429 |
At 25ᵒC |
469.5321 |
978.352 |
782.4218 |
518.2143 |
At 57ᵒC |
Noted the Table 2 yank coefficient article sawdust powder reinforced
Composite and for percentage ratio 12% and 22% possess a higher elasticity coefficient of polymer material from that bracing with sawdust, fibers work as impediments to break down that sawdust powder bear the bulk of the spotlight stress on Composite material (Thomason, Yang, & Meier, 2014), this disability over the interface between the fibers of sawdust and the basic material of unsaturated ester, as well as impediments depending on the weight percentage ratio of sawdust and the method of propagating through the material.
With percentage weighted of 32% have less elasticity coefficient of polymer material before reinforces this might be interpreted that basic material inadequate to link these chains and distributed evenly within the polymeric composite concentration leading to weakness in the overlapped structure, the increase in temperature leads to disintegration bonds between the molecular chains to the base material and thus become soft and great activity occurs and weaken in their resistance leading to low values of the yank coefficient with increase of temperature to 57ᵒC
Impact Strength(I.S)
The examination the Impact Strength give accurate indications descriptive image of strength of materials and resistance to fracture under stress at high speed (Balos, Pilic, Markovic, Pavlicevic, & Luzanin, 2014; Rajaei, Kim, & Bhattacharyya, 2018), Impact Strength is calculated using the relationship Equation 4 ,
Area: Cross-section of the sample space when breaking.
The durability of Impact Strength depends on the amount of weight ratio, and base material reinforces the material and the degree of conjunction and overlap between materials as well as on the nature of the particles so that whenever the energy needed to break the sample before it consolidation (3.486 Joule/m2).
The results obtained showed and illustrate in Table 2 that when reinforced polymeric material with sawdust the energy required to break the polymer is increasing because of fibers with various kinds stored almost of the active elastic strain energy of most article overlapped, because they bear the bulk of stress Damocles relative to the base material. Thus, the fiber works on the distribution of stress on the larger size and reduce the likelihood of stress concentration at a particular area as well as they serve as impediments to breakage and inhibit the growth of small cracks caused by impact (Al-Mosawi, 2009; Mohammadi & Moghbeli, 2018).
Hardness(B. Hr.)
Hardness define is the resistance of the material to scratching or penetrate, and there are several different global standards to calculate the hardness of plastic material; the most common uses are Brinnell hardness and Rockwell hardness. Slow rate penetration occurs at the surface of the sample during the test and while drop force leads to topical creep, and after the demise of the influential power gets restored slow relatively in testing this change impact the dimensions adopted in calculation of material hardness, to prevent that we should abide by specific period time during drop force on the model surface (Lyapina, 2016).
hardness property consider as an important surface mechanical properties and may be the polymeric materials expose l to scratching and penetration in Genera by hardest equipment during use in application areas (Tong, Mouritz, Bannister, & J. Prosthet. Dent, 2002), uses of Brinnell method to calculate the hardness of composite material, you can extract the values of hardness from Equation 5 (Gowda et al., 2018; Liu, Deng, & Zhang, 2017; Xavier, 2015)
While:
P= exposed load(Kg)
D= steel ball diameter
d= Ball notch diameter
t= notch depth
Table 2 review the values for overlapping material before and after reinforced with sawdust fibers, and notes that the hardness values have improved after reinforced unsaturated polyester with sawdust fibers, the hardness coefficient increase with increasing of fiber ratio related to overlapping caused from packing between unsaturated polyester and sawdust fiber that lead to reduces the movement of molecules to the polymer and therefore increase its rigidity which leads to greater resistance to scratching (Asi, 2018).
Compressive Resistance(C.S)
This resistance shows how material sustain when subjected to fast static compaction before the break, and the high values indicate large forces of cohesion between particles of material. The examine of material compressive resistance consider the tests which complete the picture about the strength and sustain of the polymer, the strengthen of polymers by fiber leads rise the values of compressive strength of composite material resulting from this reinforced and its clear through the Table 3 representing compressive strength test of unsaturated polyester polymer-reinforced by sawdust fiber, Where compressive resistance rises sharply when reinforcement with sawdust fibers and increase the reinforcement ratio, and it depends on the type of reinforcement material in basic material (Mohammadi & Moghbeli, 2018) due to load distribution on the fiber and unsaturated polyester adhesion force with sawdust fiber. In general, the compressive resistance Defined as the maximum stress sustain by solid under vertical pressure (Agarwal, Patnaik, & Sharma, 2014).
Polymer after reinforced (sample3 32%wt) |
Polymer after reinforced (sample2 22%wt) |
Polymer after reinforced (sample1 12%wt) |
Polymer before reinforced |
mechanical properties |
---|---|---|---|---|
6.754 Joule/m2 |
5.132 Joule/m2 |
3.876 Joule/m2 |
3.25 Joule/m2 |
Impact Strength |
84.1 Kg/mm2 |
71.2 Kg/mm2 |
64.5 Kg/mm2 |
32.6 Kg/mm2 |
Hardness Test |
10.432Kg/mm2 |
7.121 Kg/mm2 |
5.231 Kg/mm2 |
3.452 Kg/mm2 |
Compression Test |
Diffusion Coefficient × 10-12 m2/sec |
Acid medium type |
|||||
---|---|---|---|---|---|---|
Reinforced polyester unsaturated |
Non-Reinforced polyester unsaturated |
|||||
1.5 N |
1 N |
0.5 N |
1.5 N |
1 N |
0.5 N 1 |
|
41.05 |
38.12 |
36.74 |
36.80 |
25.60 |
23.4 |
HCl |
46.26 |
37.56 |
37.78 |
42.65 |
39.92 |
33.21 |
HNO3 |
43.16 |
36.53 |
29.12 |
42.24 |
33.06 |
28.54 |
H2SO4 |
Effect of acidic solutions on physical properties of unsaturated polyester before and after randomly reinforced with sawdust fibers
The resistance of the polymer depends on the nature of the polymer and the type and nature of the medium immersed in. The purpose of studying polymer degradation is to identify the impact of various liquids.
It was found that the absorption process that happens to polymers and composite materials when immersed in water or solvent or when exposed to moisture in the environment weather obey de distribution low
It is meaning the mas of water, or the solution absorber is increased linearly with the square root of the time gradually and slowing down until you reach saturation (Ewaid & Abed, 2017; Salama, Hassabo, El-Sayed, Salem, & Popescu, 2017).
The absorber solution concentrated within basic material, causing a swelling in the polymer and leads to a change in its dimensions because these solutions are work as elastomer to polymeric material (Dobah, Ghazzawi, & Bourchak, 2015).
It has been noted that when immersing samples in solutions the weight of samples increases with immersing time due to polymeric material(when being in direct contact with the liquid)especially in low molecular weight liquid (Al-Mosawi, 2009).
so liquid molecules will try to pass quickly through the phase of polymer beginning with filling micro gaps, involves in this process keep away of the polymeric chains from each other.
The first de distribution low applies in the stable state, meaning there is no concentration change with time (Hasan & J.Majeed, 2012). The increase in mass percent ratio(Weight Gain %) was calculated using Equation 7
M1= mass in gram of sample before immersing.
M2= mass in gram of sample after immersing.
As you coefficient of diffusion as well as Diffusion Coefficient calculated from relationship charts between the increase in mass and the square root of time of according to the second low of de distribution by using Equation 8
K= slope of the linear part of the curve of increasing in mass with the square root of time.
B= thickness of the sample.
M∞= (Water content when you reach saturation state) the highest value gain in weight.
The Figure 8; Figure 7; Figure 6; Figure 5; Figure 4; Figure 3 illustrate the relationship between the percentage of increase in absorption mass and the square root of time for unsaturated polyester (reinforced and no) with sawdust which immersed in the acid solutions of (HNO3, HCl, H2SO4) acids.
Through these figures notes the apparent increase in polymer mass reinforced by sawdust from non-reinforced polymer with increasing the immersion time the reason for this is that the polymer degradation works to break down and decipher the interconnections between unsaturated polyester and sawdust, so these areas as a point centers to pass solutions throw composite material, therefore, reinforced polymer have higher absorption ability than non- reinforced polymer. Increase in absorption ability can be noted as increasing in acidic solution concentration.
When reinforced material absorbs the acidic solution the bonds of material will be destroyed, and holes are appeared as a result of this step, these holes filed with acidic solution, so they will be the centers allowing the solution to enter to the inside of reinforced material (Hasan & J.Majeed, 2012).
Note that the Table 4 values of the diffusion coefficient of unsaturated polyester before reinforced is lower than that after reinforced, so diffusion coefficient after reinforced increase with the increment of acid concentration because acids effect on the internal bonds and sawdust fiber cause to increment of bonds degradation (Abd-Ali, 2012; Ibraheen, Hussein, Abed, & Ali, 2017; Salih, 2009; Zheng, Ning, & Zheng, 2005).
Conclusion
By conducting tests on samples: found increased in yank coefficient value after reinforced with sawdust powder, while decreasing with increased temperature. Either the mechanical properties like hardness, impact, compressing and ability to loads resistance of reinforced material with sawdust powder when compared with those before reinforced. Also, noted an increased in the value of both the absorbency and diffusion coefficient of reinforced polymer with sawdust compare with non-reinforced polymer because of chemical influences on overlapping material which depends on the chemical composition, And found there a difference between values of diffusion coefficient of polymer before and after reinforced with increasing the concentration of acid in the solution because increase the influence of the acid on binder in polymer and sawdust leading to their degradation.